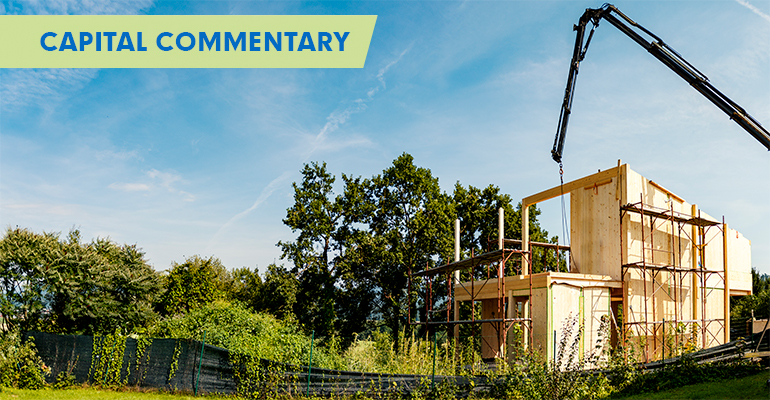
The median price of an existing home skyrocketed for the 11th straight month in May, hitting an all-time high of $419,300!
That’s right —it’s the priciest peak ever recorded by the National Association of Realtors®.
But here’s the kicker: With a staggering shortage of 3 to 6 million homes nationwide, we desperately need more inventory to satisfy the surging demand for shelter.
So, what if there was a game-changing, cost-effective way to build homes faster and more efficiently?
Enter the manufactured and modular housing champions, who are shouting triumphantly, “There is a way” from the rooftops!
Yes, but some experts have their doubts.
In the next two issues of Capital Commentary, we dive into the evolving world of factory-built homes and explore the crucial policy shifts needed to supercharge their role in solving the housing crisis.
- Modular housing is the subject of this issue.
- Manufactured housing will be the focus of our next one.
1-Big Thing: Can Factories Solve the Housing Shortage?
One of the world’s preeminent modernist architects predicted the future of home construction:
Housing “will be created no longer at the construction site, but instead at specialized factories with all the ready-to-assemble components.”
The architect? Walter Gropius. The year? 1926. Sadly, his vision for the future is still in the future.
Why it matters: Factory-built homes are faster to construct, use less labor, reduce building-material waste and can be considerably less expensive than site-built homes.
On the other hand, current home-building practices aren’t keeping up with productivity gains in most other industries. As the New York Times notes:
“While nearly every other industry has become more productive since 1968, productivity in homebuilding — the amount of work done by one worker in one hour, essentially — has declined by half.”
Factory-built homes include:
- Modular homes, constructed off-site, assembled on-site and attached to a permanent foundation. They are classified as real property.
- Manufactured homes, constructed in factories and assembled on a permanent chassis. They are subject to U.S. Department of Housing and Urban Development (HUD) design and fabrication standards. Depending on who owns the land underneath, many are titled as personal property.
By the numbers: The advantages of factory-built homes haven’t translated to their sales.
- Modular construction is used in less than 4% of U.S. homes.
- HUD-code manufactured housing represents just 6% of U.S. housing stock.
The bottom line: The U.S. needs more housing, and we need it quickly. Factory-built homes can help the country meet both objectives. Policymakers and manufacturers must identify and solve barriers restricting their contribution to our housing stock.
2. Why Modular Succeeds Abroad
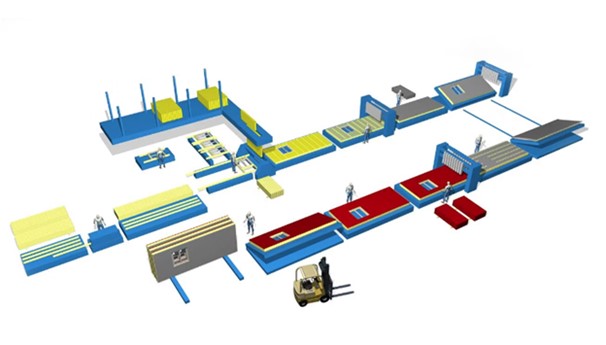
Gropius wasn’t wrong. But he was too optimistic about factory-built homes’ contribution to the U.S. housing supply.
Why it matters: Modular housing is a rousing success in other nations. And we could learn from their techniques and regulatory structures to grow modular’s footprint in the U.S.
By the numbers: Nearly all Japanese construction is industrialized, and 15% of homes are prefabricated in steel. In Sweden, 45% of construction is industrialized.
- Lindbäcks Bygg, a family-owned modular builder in Sweden, is emblematic of the success of industrialized homes, as the New York Times described.
“Everything in the factory was oriented around one main line — a slow-moving conveyor belt on which finished components were assembled into fully formed modules. The main line was the spine. More time-consuming subassemblies — shorter lines with machines building floors, walls, ceilings and so-called logistics, like countertops and cabinets — fed into the spine like ribs. One boxy unit was completed every 30 minutes. The units could be connected to create apartments of different sizes and floor plans.”
The 75-year-old company can produce more than 25,000 square feet of turnkey housing per week.
One reason modular construction has succeeded overseas and failed here might be due to regulatory practices:
Building codes in the U.S. try to make buildings safe by prescribing exactly what materials must be used and how (a prescriptive code). In Sweden, the government does this by setting goals and letting builders come up with a way to achieve them (a performance code).
- In Sweden, regulators ensure the manufacturing process meets safety and sustainability goals for constructed homes.
- In the United States, each residential building needs to be granted a permit. Moreover, inspectors eye one home at a time during the construction process. As the Times notes:
“That contributes to a stop-and-go pace that frustrates pretty much everybody except lenders who get interest on financing.”
3. Jumpstarting Modular Construction in the U.S.
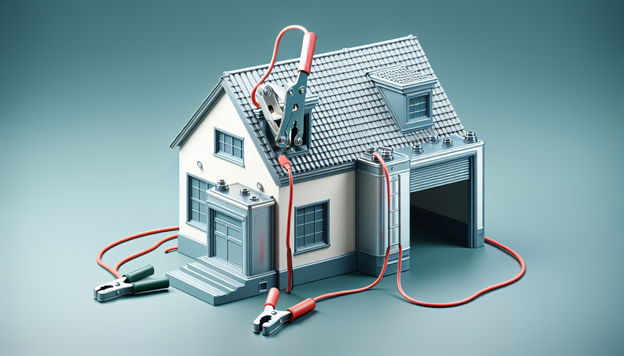
The advantages of modular building could create a 16% savings in total costs and a 39% schedule compression compared to conventional construction, according to the Modular Building Institute.
In 2023, the Harvard Business Review (HBR) published a deep dive into modular housing that confirmed projections of a shorter schedule.
The cost savings? Not so much.
What they’re saying: HBR noted, “The expense of producing boxes is still only approximately half of total project costs, and transportation (to the site) can be a budget killer.”
For modular construction to significantly impact U.S. housing growth, experts recommend the following:
- Expand financial resources to encourage modular building, including tax-exempt bonds and federal grants.
- Standardize building codes and regulations. Housing industry officials took a notable first step in this direction in 2023 when the International Code Council and the Modular Building Institute announced a national initiative to adopt standards for off-site construction.
- Expand the capacity of modular factories.
“A friend of mine did a federal study that if we wanted to get to 10% of the market, you’d have to build 600 factories. That’s like a $15 billion effort. You don’t do (that) without some kind of government support.”
Ken Simler, President and CEO, Impresa Modular, at the 2024 Summit of Housing Supply Solutions.
That’s not all: Those changes would help, but so, too, would an effective public relations campaign to improve the awareness and reputation of modular homes, particularly to differentiate them from HUD-code manufactured homes.
4. Hot Dogs and Houses

Costco is breaking the mold of big-box stores and creating molds for modular housing to sit atop a new Los Angeles warehouse.
To expedite the construction of a new store on the site of a former hospital, Costco is building 800 apartments, of which 184 will be set aside as affordable housing. Costco will use modular construction methods to build the housing units.
Why it matters: Costco can earn incentives by building a mixed-use development, but housing must comprise at least two-thirds of the total square footage. With a 185,000-square-foot Costco at street level, that adds up to a lot of residential space to fill.
Developer Thrive Living will use prefabricated apartment modules that can be easily transported. The modules must fit under bridges and on the back of trucks, so the dimensions will be small.
What they’re saying:
“If done right and embraced by locals, developers, big box retailers and public officials, the project could be a novel model for future build-outs statewide.”
SFGate.com
Call it the new Costco Combo: Affordable housing and the always popular $1.50 hot dog and soft drink special. It just might be coming to a store near you.
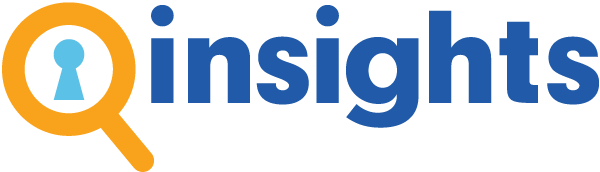
About Arch MI’s Capital Commentary
Capital Commentary newsletter reports on the public policy issues shaping the housing industry’s future. Each issue presents insights from a team led by Kirk Willison.
About Arch MI’s PolicyCast
PolicyCast — a video podcast series hosted by Kirk Willison — enables mortgage professionals to keep on top of the issues shaping the future of housing and the new policy initiatives under consideration in Washington, D.C., the state capitals and the financial markets.
Stay Updated
Sign up to receive notifications of new Arch MI PolicyCast videos and Capital Commentary newsletters.